What is Rapid Tooling?
Rapid tooling is a rapid prototyping technique primarily used in place of conventional tooling to produce functional molds at lower costs and shorter lead times. This manufacturing method combines rapid prototyping techniques with the digital tenacity of electronic CAD data files to create a production mold instead of a part. The molds produced with rapid tooling services are often referred to as hard tooling. They are used in making hundreds to thousands copies of a part, serving as the “original” in plastic injection molding, and pressure die casting operations.
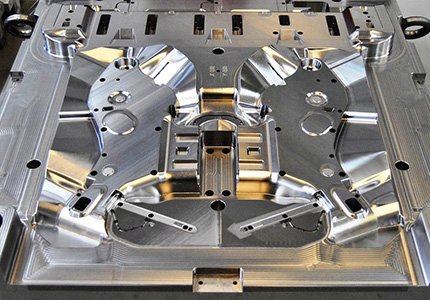
Advantages of Rapid Tooling
Rapid tooling holds several advantages over the conventional tooling process. Some of the key benefits of rapid tooling operations include:
1. Rapid Turnaround
Speed is the primary attribute of rapid tooling. Using the digital CAD file, and digital manufacturing, rapid tooling can make molds and dies for low to mid-volume production operations faster than conventional tooling. Rapid tooling operations can reduce around 40-60% of the traditional molding lead-times.
2. Precision
Precision is imperative in tooling because your molds will be used to manufacture other copies. Rapid tooling uses digital technology that can fabricate tooling with high precision. This way, you can be rest assured on the accuracy and detail of rapid tooling, and confident in your tooling investment. Rapid tooling molds can be finished in various ways, including texturing, polishing, and bead blast blasting.
3. Complex geometries
Rapid tooling allows you to innovate with freedom. With our digital capabilities integrated into our rapid tooling process, we can create mold tools with complex shapes and intricate patterns. Rapid tooling can also easily be modified to accommodate design changes and modifications.
4. Low-cost tooling
Rapid tooling can work around budgetary constraints and use aluminum tooling to manufacture low-cost molds for low to mid-volume production runs. Rapid tooling is around 40-50% cheaper than traditional mold tooling.
Rapid Tooling Applications
• Mold making
Rapid tooling can make mold tool components, cores, and cavities for plastic injection molding and die casting operations in up to 40 percent less time than conventional processes.
• Rapid prototyping & Low-volume production
Low-cost tooling through aluminum materials can help you make molds and dies for quick prototyping and low-volume with end-used quality.
Rapid Tooling Technology
• CNC Milling
CNC machining operations can incorporate intricate design, detail, and textures into the mold tool.
• Electro-discharge machining
EDM is ideal to create the unconventional features that traditional milling machines cannot produce. It is widely used to produce molds and it can be precise.
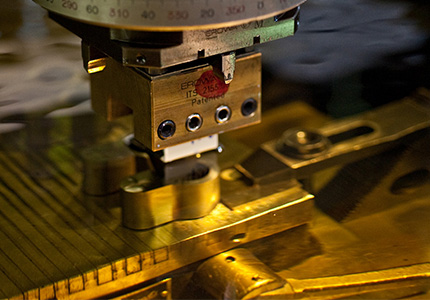
Industries
Rapid tooling is used in virtually every aspect of industrial manufacturing, low-volume production, and product prototyping. The following industries can use rapid tooling:
• Automobile
• Aerospace and Aircrafts
• Construction
• Consumer Electronics
• Consumer products
• Military/Defense
• Energy and Power
• Medical
• Transportation
• Education
Material options
At Premium Parts, rapid tooling is mostly accomplished with Aluminum and Steel alloys. Here are some of the properties of both type of materials:
Aluminum
Aluminum is the ideal choice for low-cost rapid tooling. Aluminum mold is often used when making molds for low-volume runs that may not produce more than around 10,000 shots in its entire cycle. Using aluminum can reduce tooling costs by up to 25%.
Aluminum is an excellent option because of its dimensional stability and heat-dissipation properties. Aluminum 7075 is the ideal fit for very low volume requirements, making up to 10,000+ parts. However, the parts will not boast the best of texture, gloss, or surface finishes. Its softness means improved machinability and shorter lead-times. At Premium Parts, we use the 7075 for on-demand tooling operations.
Steel
Steel is a sturdy, high-quality, and highly efficient tooling material option. Steel molds are stronger and will usually have a longer lifespan than aluminum alternatives. It is generally used for high-volume production and is more expensive to produce with longer turnaround times. Steel molds can last for around 50,000 shots. The steel P20 is widely used in rapid tooling, especially when the parts can make do with regular surface finishes. Depending on the part geometry, size, and resin structure, high-quality P20 molds can make up to 150,000 parts. The NAK80 and S136 are excellent for rapid tooling molds, where the parts will require a glossy or high-quality finish. Due to its increased hardness, steel tooling can make up to 400,000+ parts.
Finishing Services
Depending on the material used, the material to be molded, cast, and design geometry, Premium Parts can finish your parts in various ways. Some of our finishing solutions for rapid tooling include:
• Texturing
• Commercial Polishing
• Mirror Polishing
All our tooling solutions are designed with considerations around the surface finish guidelines of plastic injection molding and pressure die casting.
Why Choose Us
• Tooling Quality
We use the certificated materials and manufacturing capabilities to make high-quality rapid tools. We ensure that all our molds have tight tolerances and smooth finishes to facilitate your parts’ ejection from the mold.
• Family molds
Premium Parts can use rapid tooling to make functional multi-cavity molds for your end uses. Our family molds are ideal for creating multiple components of a part in identical material. Family molds are a great way to save costs and time arising from assembly operations.
• Consistency and Repeatability
We can manufacture any amount of tooling for your end-use parts without compromising on consistency and quality.
• Capacity and Range
Premium Parts can source and work with a handful of aluminum and steel tooling alloys that fit both small, mid-range, and mass production end uses. Our Rapid tooling is ideal for working with budgetary limitations.
Rapid Tooling FAQs
1. How long can you store our tooling before the next order?
We can store your tooling for up to 5 years, after your last order.
2. If our tooling was broken before the expected quantity molded, what can you do for us?
Generally, if our tooling was running out of its’ tooling life, we can remake another new mold free of cost.
3. Can I export my tooling?
Please let us know the tooling would need to be exported when you inquiry. We would need to quote the independent mold so you can export it.
4. What’s the typical life of rapid tooling?
It bases the material we used for mold making. For mold with aluminum, it can mold around 10,000 units. For mold with steel, it can mold 50,000 to 100,000 units roughly.